04.06.2024
From A to Z: Understanding Hydrogen Stacks and Their Applications
Pursuing more sustainable and environmentally friendly energy solutions in today's rapidly evolving business landscape is not optional. Companies across various industries are seeking innovative ways to reduce their carbon footprint, and one technology that holds immense promise is hydrogen production. Specifically, we will explore the intricacies of hydrogen stacks, a key component in the journey toward a greener and more efficient future.
The Rising Prominence of Green Hydrogen
Hydrogen has gained widespread attention as a clean and versatile energy carrier that has the potential to revolutionize multiple sectors, including transportation, industrial processes, and energy generation.
Its appeal lies in its high energy density, zero greenhouse gas emissions when used, and the ability to store and transport energy effectively. As companies look for ways to decrease their carbon emissions, understanding the intricacies of hydrogen stacks becomes essential.
The Role of Hydrogen Stacks
Hydrogen stacks, also known as electrolyser stacks, are the heart of any hydrogen production system. These stacks are a complex assembly of components designed to facilitate the electrolysis of water, splitting it into its constituent elements—hydrogen and oxygen—using electrical energy. The hydrogen produced can then be harnessed for various applications, making stacks a pivotal element in the journey towards sustainable hydrogen-based solutions.
The Anatomy of an Electrolyser Stack – Main components
To comprehend a hydrogen stack's functionality, dissecting its components and understanding their roles within the system is essential. Here they are:
Electrodes: The stack typically consists of two electrodes, one positive (anode) and one negative (cathode). These electrodes are usually made of materials such as titanium or nickel, coated with a catalyst material to enhance the electrochemical reactions that occur at their surfaces. However, electrodes don’t necessarily need to use precious metals, At Stargate, we build upon the best aspects of proven alkaline technology and complement it with breakthrough materials. This results in a completely new class of electrolysers: ceramics-based alkaline electrolysers, that have high current densities and high efficiencies, yet contain no precious metals. This results in significantly lower hydrogen production costs and makes the electrolysers affordable for the end-users.
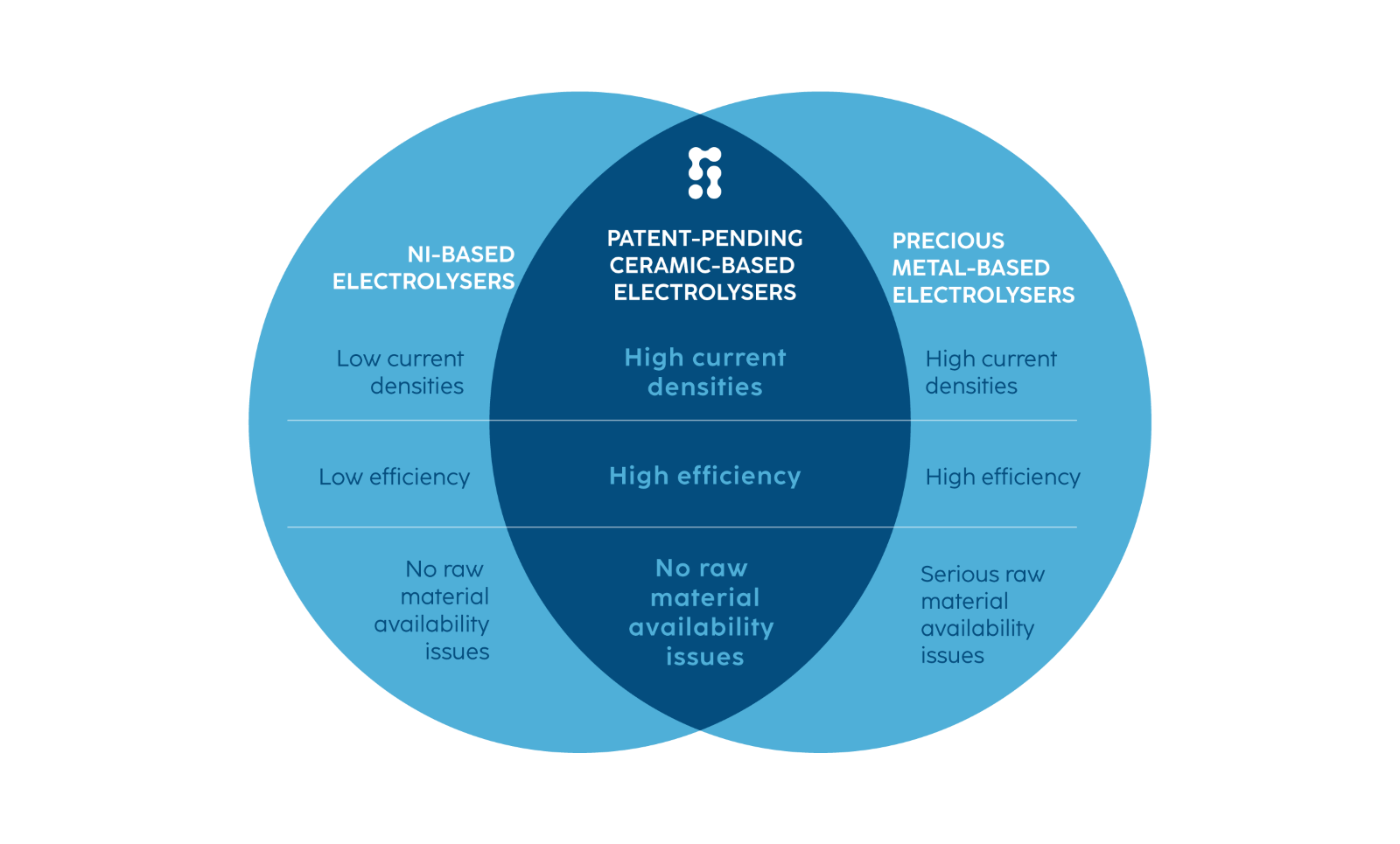
Electrolyte: The space between the electrodes is filled with an electrolyte, a substance that allows ions to move freely between the anode and cathode. Electrolytes can be either solid or liquid. Commonly used electrolyte in alkaline electrolysers potassium hydroxide (KOH) solution.
Current Collectors: Current collectors are essential for efficient distribution of electrical current throughout the stack. They help ensure that electrolysis occurs evenly and effectively.
Separator Plates: Separator plates are placed between individual cells within the stack, preventing mixing of gases and ensuring a clear path for the generated hydrogen and oxygen to reach their respective collection points.
Gaskets and Seals: Gaskets and seals prevent leakage of electrolyte and gases, maintaining the integrity of the system. Proper sealing is crucial to the safety and longevity of the stack.
Pressure Management System: In some electrolysis systems, pressure management is necessary to control the pressure of the hydrogen and oxygen gases, which may vary during the operation of the stack.
Cooling System: To prevent overheating and maintain an optimal operating temperature, stacks incorporate a cooling system that dissipates excess heat generated during electrolysis.
Power Supply: The power supply, usually in the form of direct current (DC), provides the electrical energy required for the electrolysis process.
The Electrolysis Process
Now that we have a grasp of the components that make up a hydrogen stack, let's dive into the intricate electrochemical reactions that take place within the stack during electrolysis. This is the process through which water is converted into hydrogen and oxygen gases.
Electrolysis of Water: When a direct current (DC) is applied across the anode and cathode, water (H2O) is split into its constituent elements:
Anode Reaction: 2H₂O → 4H⁺ + 4e⁻ + O₂
Cathode Reaction: 4H⁺ + 4e⁻ → 2H₂
Hydrogen Generation: Hydrogen gas (H₂) is produced at the cathode, where electrons (e⁻) are supplied, and protons (H⁺) are reduced to form hydrogen molecules.
Oxygen Generation: Oxygen gas (O₂) is generated at the anode, where water molecules are oxidized to produce oxygen gas and release electrons.
Gas Separation: The separator plates ensure that the generated hydrogen and oxygen gases remain separate and are collected separately.
Gas Collection and Storage: The collected hydrogen gas is then processed for storage, while the oxygen gas is often vented safely into the atmosphere.
What Makes a Good Hydrogen Stack?
While the principles of electrolysis are consistent, not all hydrogen stacks are created equal. The quality and efficiency of a hydrogen stack play a crucial role in determining the success and viability of a hydrogen production system. On the next paragraphs you will learn what are the key factors that define a good hydrogen stack.
Efficiency is the cornerstone of a good hydrogen stack. An efficient stack will maximize the conversion of electrical energy into hydrogen gas while minimizing energy losses, often in the form of heat. Efficiency is typically expressed as the ratio of electrical energy input to the energy content of the hydrogen produced, known as the electrical-to-chemical energy conversion efficiency.
Hydrogen stacks are subjected to demanding conditions, particularly high temperatures and electrical currents. A durable stack should be able to withstand these conditions over an extended period without significant degradation. Materials selection, cooling systems, and corrosion resistance are critical factors that influence durability.
Consistency in hydrogen production is essential for commercial applications. A good stack should exhibit stable performance over time, producing hydrogen at a predictable and reliable rate. Variability or fluctuations can lead to inefficiencies and increased maintenance requirements.
The ability to scale up or down is crucial, especially for companies with fluctuating hydrogen demands. A good stack should allow for easy scalability to meet changing production needs without excessive modifications.
Safety is a huge concern in any hydrogen production process. A good stack should incorporate safety features, such as reliable seals and pressure management systems, to prevent gas leaks or other potential hazards.
A low-maintenance stack is highly desirable, as it reduces downtime and operational costs. A good stack design should minimize the need for frequent servicing and part replacements.
While the initial cost of a hydrogen stack is a consideration, the overall cost-effectiveness should be evaluated, taking into account factors such as efficiency, durability, and maintenance costs over the stack's lifespan.
Download our Hydrogen Stack integration guide:
If you are a decision maker in an engineering company looking to become a Hydrogen Stack integrator our latest guide will be a high-value asset. Download the guide here and ensure you will make informed decisions to achieve optimal efficiency.
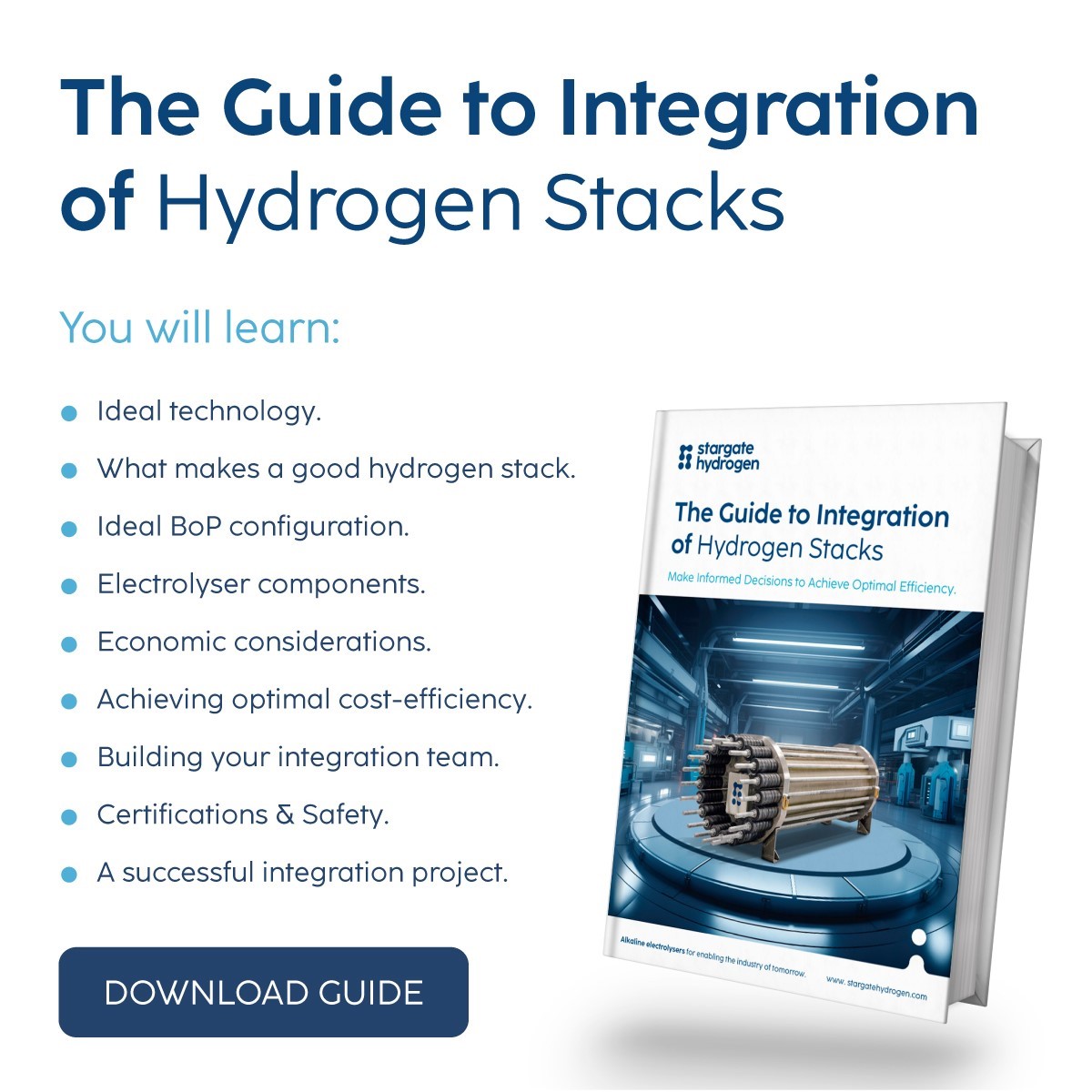
Applications of Hydrogen Stacks
Hydrogen stacks find applications in a wide range of industries, serving as a fundamental component in hydrogen production for various purposes. Let's explore some of the prominent applications where hydrogen stacks are making a significant impact:
Hydrogen Fuel Production
One of the most well-known applications of hydrogen stacks is in the production of hydrogen fuel for fuel cell vehicles. These stacks are integrated into hydrogen refuelling stations, where they electrolyze water to produce high-purity hydrogen gas, which is then either compressed or liquefied and stored for vehicle refuelling.
Industrial Processes
Hydrogen is an essential feedstock for various industrial processes, including the production of ammonia, methanol, and steel manufacturing. Hydrogen stacks play a crucial role in providing a sustainable source of hydrogen for these applications, reducing the carbon footprint of industrial operations.
Power-to-Gas (P2G)
Power-to-gas is a cutting-edge technology that converts excess electricity, often from renewable sources like wind and solar, into hydrogen or further into syngas or methane for energy storage. Hydrogen stacks are pivotal in this process, allowing surplus electricity to be transformed into a storable energy carrier, which can be converted back into electricity when needed.
Backup Power Generation
Hydrogen stacks can also serve as a reliable source of backup power generation, especially in areas where grid reliability is a concern. These stacks can be used to produce hydrogen for fuel cells, providing emergency power in critical infrastructure settings.
Key Takeaways
Hydrogen stacks, or electrolyser stacks, represent a pivotal component in the quest for sustainable hydrogen production and its applications across various industries. These intricate systems are designed to split water into its constituent elements, hydrogen and oxygen, using electrical energy. A good hydrogen stack is characterized by efficiency, durability, consistency, scalability, safety, minimal maintenance, and cost-effectiveness.
As companies and industries continue to prioritize the reduction of carbon emissions and seek cleaner energy solutions, hydrogen stacks are poised to play a central role in enabling the transition to a greener and more sustainable future. With ongoing research and development, these stacks are evolving to meet the growing demands of a changing energy landscape. The potential of hydrogen stacks is vast, and their applications are expanding, offering a promising path towards a cleaner and more sustainable future.
So, if your company is considering a move toward hydrogen-based solutions, understanding the intricacies of hydrogen stacks is crucial. By investing in quality hydrogen stacks, you can harness the power of this versatile energy carrier and contribute to a more sustainable and environmentally friendly future for your organization and the planet.
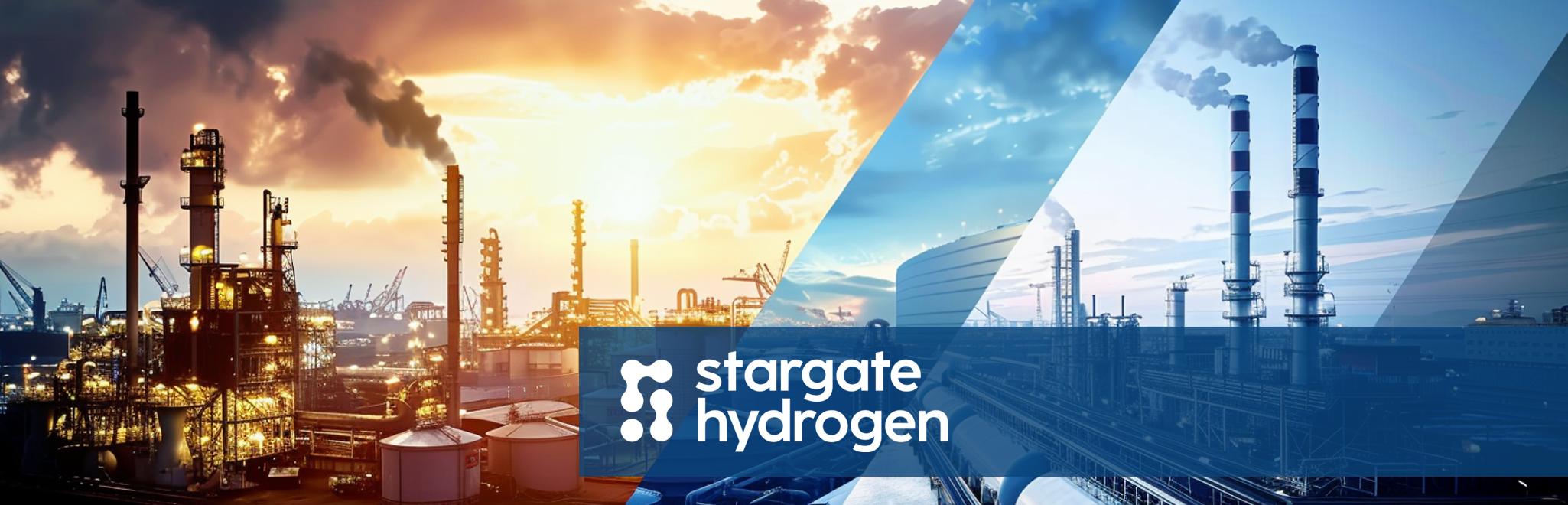