06.05.2025
How Pure Is Pure Enough? The Most Important Questions About Hydrogen Purity
Article Audio summary
If you prefer, you can listen to a summarised version of this article:
Takeaways
- Hydrogen purity is defined by the amount of contaminants in the gas.
- Different applications—from fuel cells to industrial heating—require different purity levels.
- Fuel cells, semiconductors, and pharmaceuticals demand extremely high-purity hydrogen, sometimes exceeding 99.9999%.
- Contaminants can degrade performance, damage equipment, or halt operations.
- Measurement methods include gas chromatography, mass spectrometry, and others based on international standards like ISO 14687:2025.
- Purification technologies such as PSA, palladium membranes, and cryogenic distillation are chosen based on use case and cost.
- High purity increases operational costs but prevents larger losses in efficiency or quality.
- Electrolysis produces purer hydrogen than steam reforming, especially when water quality and system conditions are tightly controlled.
- Understanding the tradeoffs of purity level vs. cost is critical for engineering and procurement decisions.
The Basics: What Is Hydrogen Purity?
Hydrogen purity is the proportion of hydrogen gas relative to other gases or particles in a given volume. It’s expressed in percentage form or "grades"—from 3.0 (99.9%) to 6.0 (99.9999%). While a single decimal point might seem minor, it can mean the difference between a working fuel cell and a system failure.
For example, in proton-exchange membrane (PEM) fuel cells, even 0.2 ppm (that is 0.00002 %) of carbon monoxide can poison the platinum catalyst, leading to permanent damage. That’s why a grade of 5.0 or higher (≥99.999%) is often the baseline in these setups.
Hydrogen Purity in Alkaline Electrolysers
Alkaline electrolysers are one of the most established and widely used technologies for hydrogen production. It operates using a liquid electrolyte—typically potassium hydroxide (KOH) — and two electrodes separated by a diaphragm. They are robust and cost-effective, but the hydrogen purity output depends on several factors specific to this setup.
At Stargate Hydrogen's Turn-key systems, our engineers chose to use the Temperature Swing Adsorption (TSA) purification method. TSA is a hydrogen purification technique that uses the temperature-dependent adsorption characteristics of gas molecules on solid adsorbents. In this process, a gas mixture containing hydrogen is passed through a fixed bed of adsorbent material—typically activated alumina, silica gel, or molecular sieves—at a relatively low temperature.
Impurities such as moisture, carbon dioxide, methane, and other trace contaminants are selectively adsorbed onto the solid surface, allowing purified hydrogen to exit the system. Once the adsorbent reaches its saturation capacity, the bed is regenerated by elevating the temperature, which desorbs the retained impurities and restores the adsorbent’s capacity for the next cycle.
TSA systems are particularly suited for applications requiring deep purification, especially where impurity levels are low and adsorption kinetics are slower, such as in post-electrolysis hydrogen conditioning or industrial gas recovery setups.
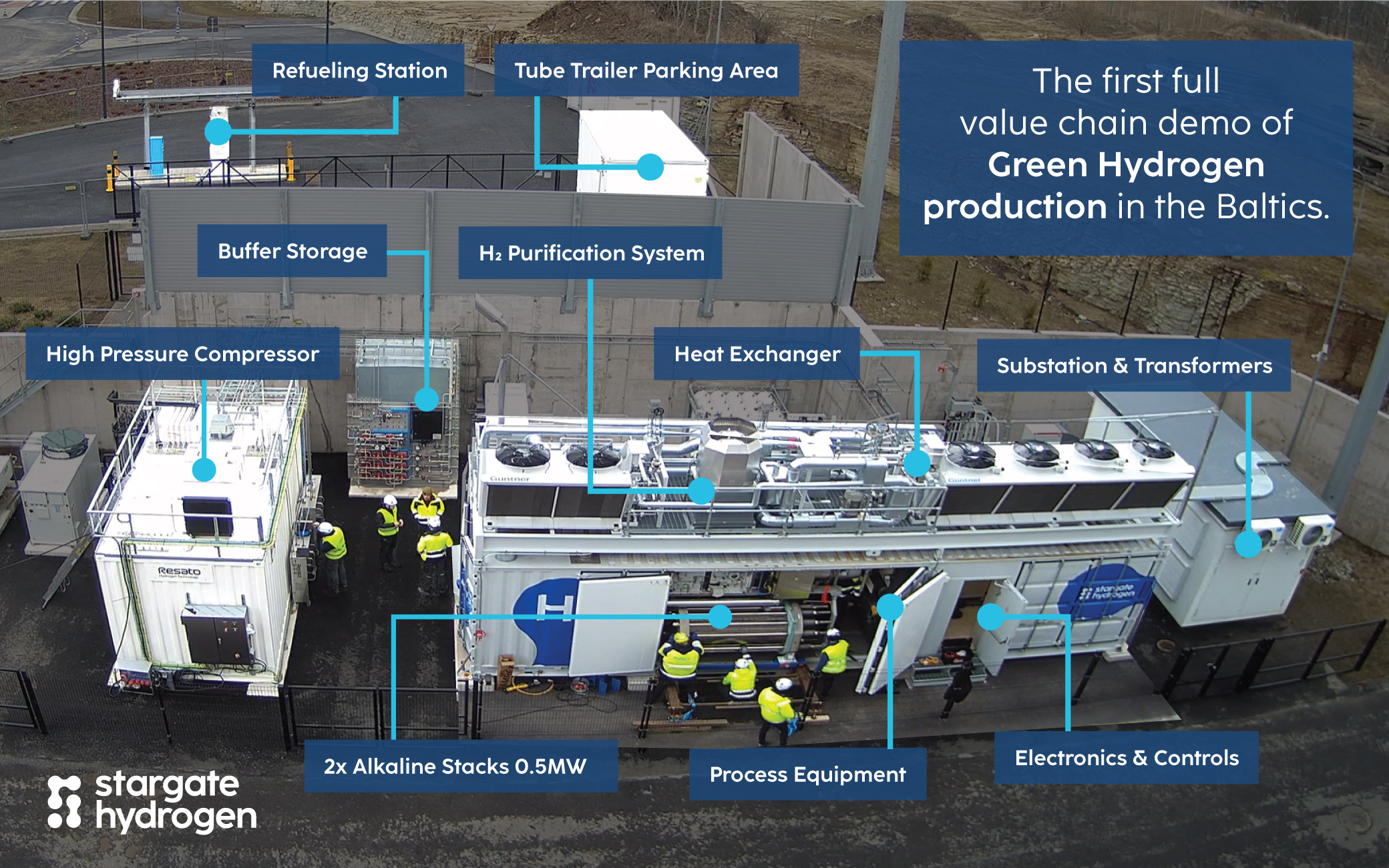
What Can Affect Purity in Alkaline Electrolysis?
Electrolyte Carryover:
- Tiny droplets of the alkaline solution can become entrained in the hydrogen stream.
- This introduces moisture and potassium-based contaminants.
Oxygen contamination:
- Due to the porous diaphragm, some oxygen from the anode side may migrate to the cathode side.
- This can result in small amounts of O₂ mixing with the hydrogen, especially under high differential pressures between the two sides
Operating Conditions:
- Higher current densities and pressure fluctuations can increase impurity levels. But in alkaline systems, such as Stargate Hydrogen's, low currents will increase impurities.
- System wear, such as diaphragm degradation, raises the risk of hydrogen and oxygen gas mixing over time.
Typical Purity Output
Most modern alkaline electrolysers can produce hydrogen in the range of 99.5% to 99.9% purity without additional purification processes. For general industrial applications, this is usually sufficient. However, for sensitive processes like PEM fuel cells or electronics manufacturing, post-purification is mandatory.
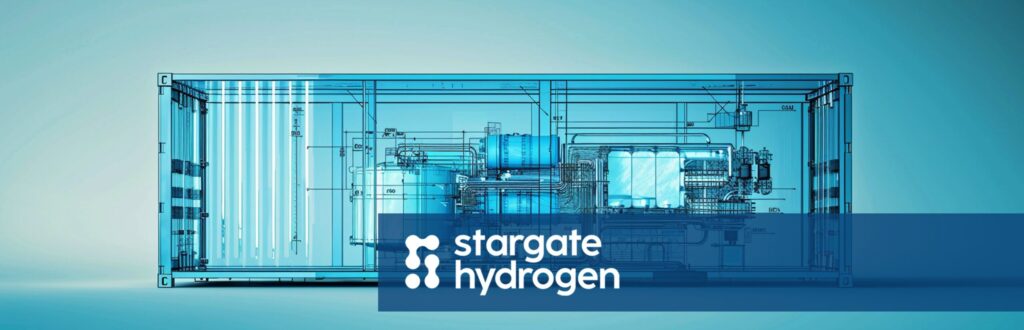
How to Improve Hydrogen Purity in Alkaline Systems
- Gas-Liquid Separators: Remove electrolyte droplets from the hydrogen stream.
- Drying Units: Eliminates moisture to prevent corrosion and downstream contamination.
- Post-Purification Stages: Add PSA units or catalytic recombiners to remove O₂ and other residual gases.
- Optimized Design: Use advanced diaphragms and better flow control to minimize crossover.
Example: Industrial Heat vs. PEM Fuel Cells
- Industrial heat applications may tolerate hydrogen at 99.5% purity, produced directly from an alkaline system.
- PEM fuel cells require >99.97% purity and cannot tolerate the O₂ or moisture levels typically found in raw alkaline output.
Interested in how Stargate Hydrogen’s alkaline systems fit into your hydrogen strategy? See our Stacks and Turn-key Systems.
Why Hydrogen Purity Matters So Much
Different industries demand different purity levels. Here’s how it breaks down:
Use Case Overview
Industry | Required Hydrogen purity | Risks due to impurities |
PEM Fuel Cells | >99.97% | Catalyst degradation (CO, NH₃) |
Semiconductors | >99.9999% | Particle contamination, O₂ traces |
Pharma | >99.999% | Wrong chemical products; contamination of final products |
Industrial Heat | ~99.5–99.99% | Combustion inefficiency, corrosion |
If a manufacturing process needs absolute consistency, like in chip fabrication, oxygen or water vapour levels must be close to zero. Even minor contaminants can disrupt delicate chemical or electrical balances.
What Contaminants Are Found in Hydrogen?
Common impurities include:
- H₂O (water vapor) – Leads to corrosion and reduced combustion efficiency.
- O₂ (oxygen) – Increases flammability risks and corrodes systems.
- CO (carbon monoxide) – Poisons catalysts in fuel cells.
- CO₂, CH₄, NH₃, N₂ – Possible other issues depending on use case
How Is Hydrogen Purity Measured?
Several methods are used to assess purity depending on the application:
- Gas Chromatography (GC): Commonly used to detect hydrocarbons and other small molecules.
- Mass Spectrometry (MS): Highly sensitive, suitable for detecting multiple different contaminants.
- Cavity Ring-Down Spectroscopy (CRDS): Ideal for detecting trace levels of moisture or complex organics.
These are governed by international standards such as:
- ISO 21087:2019 – Analytical methods for hydrogen purity.
- ISO 14687:2025 – Purity requirements for hydrogen used in fuel cells.
- SAE J2719 – Specific guidelines for PEM fuel cell vehicles.
How Is Hydrogen Purified?
Several technologies are used to purify hydrogen, each with pros, cons, and ideal use cases. Common Purification Methods:
Temperature Swing Adsorption (TSA)
- Suited for applications requiring deep purification.
- Uses the temperature-dependent adsorption characteristics of gas molecules on solid adsorbents.
Pressure Swing Adsorption (PSA):
- Most widespread method for large-scale purification.
- Uses adsorbents to capture impurities under high pressure.
Palladium Membrane Filtration:
- Allows only hydrogen to pass through.
- Achieves extremely high purity but has higher operational costs.
Cryogenic Distillation:
- Separates gases based on their boiling points.
- Suitable for bulk operations.
Electrochemical Purification:
- Useful for niche or integrated systems.
- Still under development for broader use.
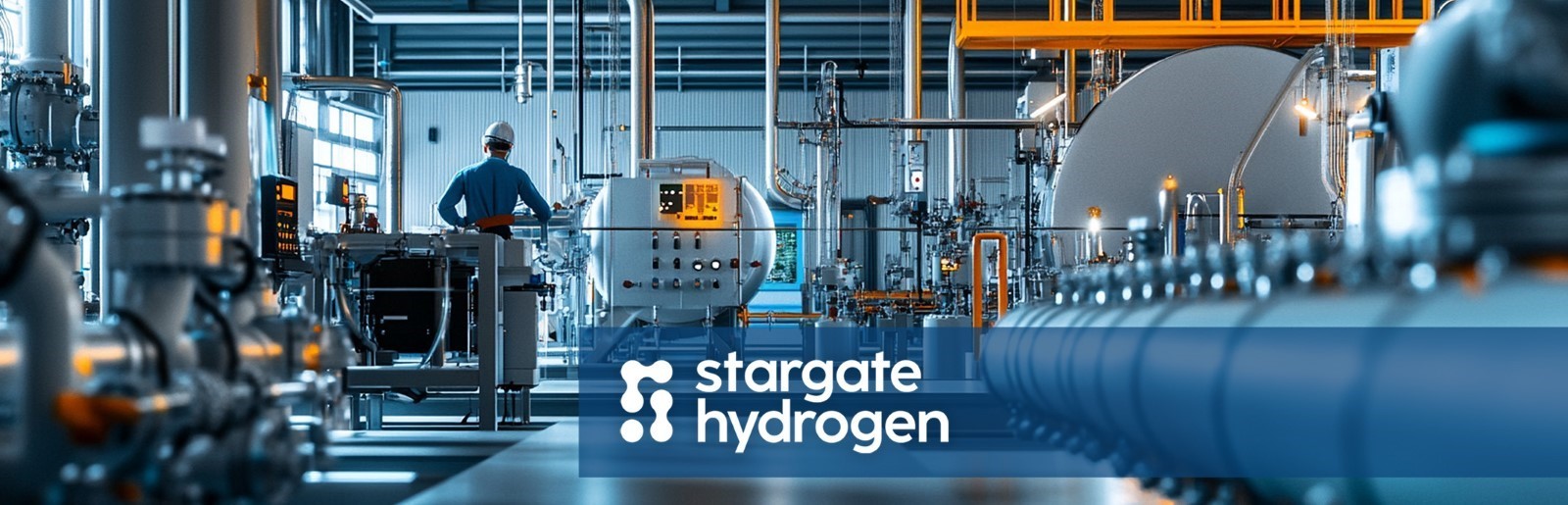
Choosing the Right Purity Level for Your Application
While it's clear that different industries require different hydrogen purity levels, what often gets overlooked is how to decide the correct grade for your own use case. This decision impacts not only system design but also procurement strategy, maintenance routines, and long-term cost modelling.
Key Factors to Consider:
- End-use equipment sensitivity: Check supplier specs for maximum allowable impurities.
- Operational environment: Humidity and temperature may affect impurity risks.
- Storage conditions: Longer storage or transport routes raise the chance of contamination.
- Regulatory and quality standards: Align with ISO, SAE, or industry-specific benchmarks.
- Total cost of ownership: Include purification, testing, and failure-risk costs in your ROI calculations.
Example Case: Pharmaceutical Manufacturing
A pharmaceutical company producing active pharmaceutical ingredients (APIs) relies on hydrogen in multiple stages of chemical synthesis—particularly hydrogenation reactions used to modify organic compounds. In these reactions, catalysts like palladium or platinum on carbon are extremely sensitive to impurities.
Let’s say they’re using hydrogen with 99.9% purity. That sounds high, but the remaining 0.1% could include moisture, oxygen, carbon monoxide, or ammonia—all of which interfere with the reaction, degrade catalysts, or introduce unwanted by-products. Moisture alone can hydrolyze sensitive intermediates or reduce yield consistency. CO can bind to the catalyst, halting the reaction altogether.
Here’s what that means in practice:
- Yield drops by 5–10%, translating into lost revenue across multiple batches.
- Catalyst lifespan is cut in half, requiring more frequent replacement and downtime.
- Regulatory compliance risks increase, especially if trace impurities remain in the final active pharmaceutical ingredients.
- Batch failures force expensive reprocessing or outright disposal.
Switching to ≥99.999% hydrogen may cost more upfront, but ensures consistent reaction kinetics, higher product yield, and longer catalyst life. Over time, these savings in process efficiency, waste reduction, and regulatory assurance far outweigh the marginal cost of purer hydrogen.
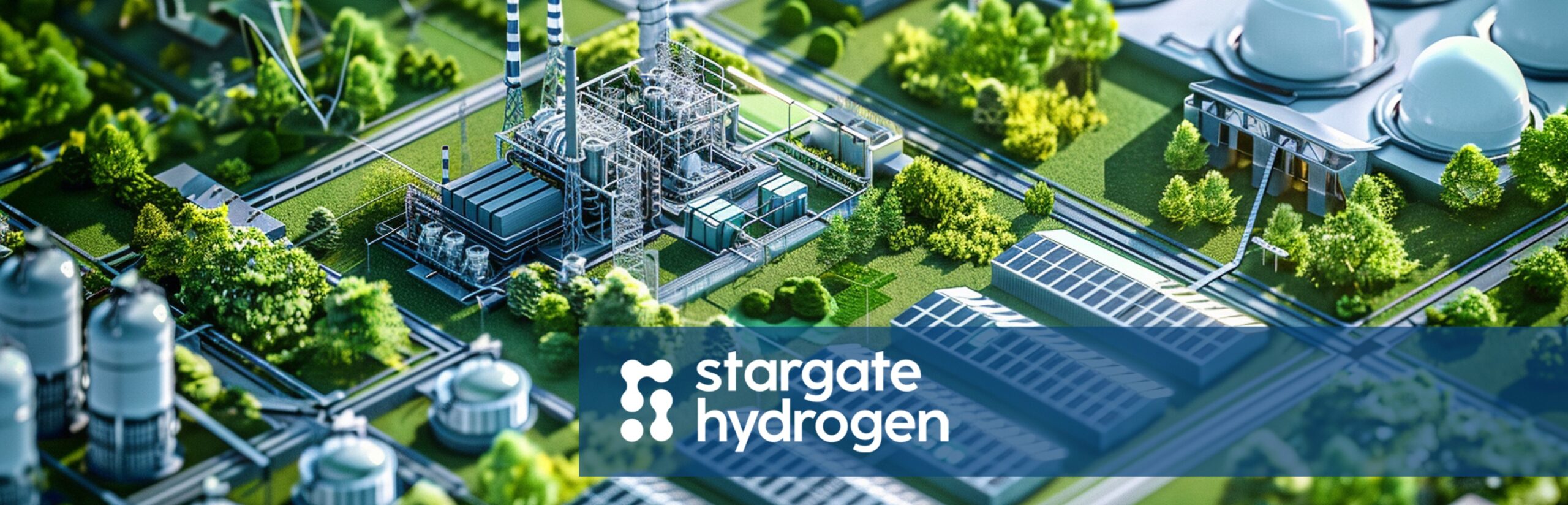
Storage and Transport: Hidden Challenges in Maintaining Hydrogen Purity
- Even after purification, hydrogen can lose its integrity during storage and transit:
- Permeation: Hydrogen seeps through some materials over time.
- System Leakage: Connections and valves may introduce ambient gases.
- Back Diffusion: Air can leak into storage tanks, especially if depressurised.
Solutions That Work
- Use storage tanks with inert linings (e.g., stainless steel, composites).
- Perform regular seal checks and pressure tests.
- Implement real-time gas monitoring during distribution.
Cost vs. Benefit: The Economics of Hydrogen Purity
What Drives Cost?
- Choice of purification technology: PSA is cost-effective at scale, while membranes are pricier but more precise.
- System maintenance: Ensuring seals and filters stay intact adds ongoing costs.
- Quality monitoring: High-end sensors and analytical tools are a significant investment.
Is It Worth It?
Yes—if the cost of using low-purity hydrogen includes a failed reaction, damaged equipment, or lost product batches.
Bonus: Curiosities and Lesser-Known Facts About Hydrogen Purity
- Ambient air is a bigger threat than you'd think: A loose valve can allow nitrogen and moisture to seep in, undermining purity within hours.
- Water quality in electrolysis matters: Deionised water ensures fewer side reactions and cleaner output.
- Online gas analysers at fuel stations: These continuously measure purity before dispensing hydrogen into vehicles.
Even small oversights can lead to large-scale issues, especially in applications demanding ultra-pure hydrogen.
Conclusion: Precision Matters when talking about Hydrogen purity
Hydrogen purity isn’t just a number—it’s a threshold for success in every serious hydrogen application. Knowing what level of purity you need, how to achieve it, and what tradeoffs to expect is essential for every R&D engineer or procurement lead working with hydrogen systems.
Each hydrogen project is different and tailored to match your needs. Contact us for a consultation with our business development team.
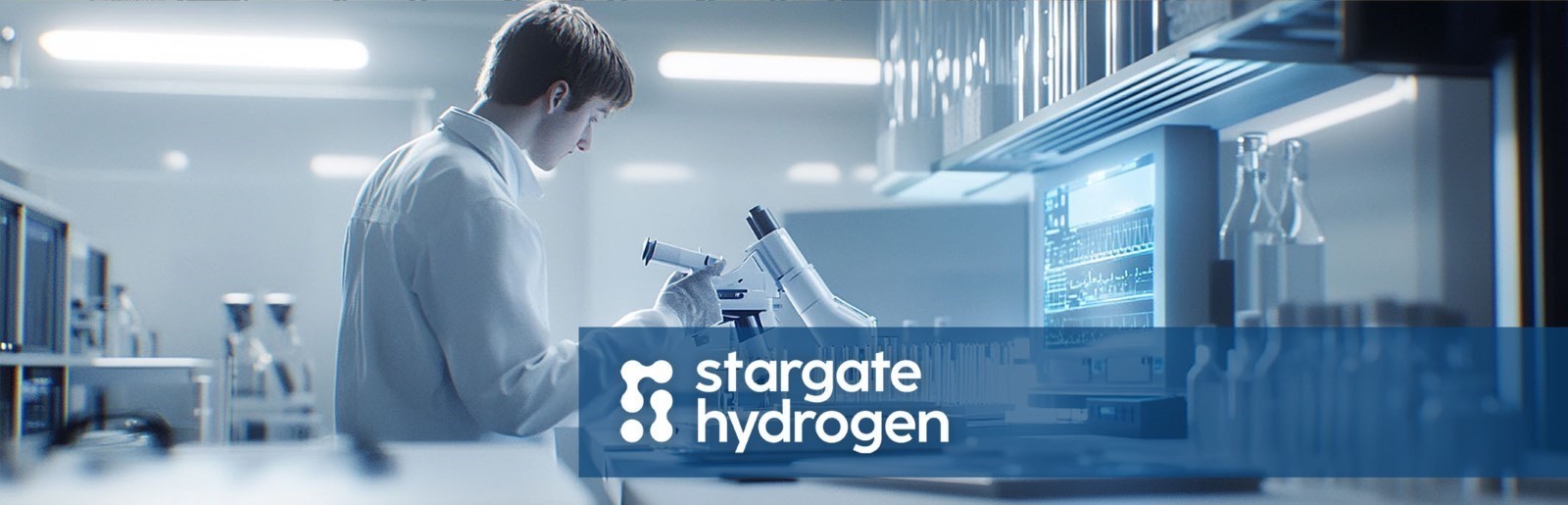